レーザーチューブ切断機驚くほど多様な機能を切り出し、プロセスを組み合わせるだけではありません。また、材料の取り扱いや半完成部品の保管も不要になり、工場の運営がより効率的になります。ただし、これで終わりではありません。投資収益率を最大化するには、店舗の業務を注意深く分析し、利用可能なすべての機械の機能とオプションを検討し、それに応じて機械を指定することを意味します。

ワークピースの形状が円形、正方形、長方形、または非対称であっても、レーザーなしでは最適なチューブ切断を実現することは想像しにくいです。レーザーシステム特に複雑な形状に関して、チューブの切断プロセスに革命をもたらしました。特に、大きなサイズのチューブを扱っており、自動化やその他の新技術を生産プロセスに導入している場合は、慎重に計画を立てて、レーザーチューブ切断あなたの会社にとって費用対効果が高いです。
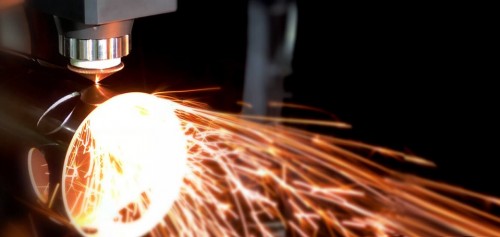
最終的には、製品の購入を決定する前に、いくつかの変数を考慮する必要があります。レーザーチューブ切断機;製品設計、プロセスの簡素化、コスト削減、応答時間は最も重要です。
製品の特徴
レーザー切断全く新しい製品デザインに応用できます。革新的で複雑なデザインはレーザーで簡単に加工でき、製品をより強く、より美しくすることができ、多くの場合、強度を犠牲にすることなく重量を軽減できます。チューブレーザーは、チューブの組み立てプロセスのサポートに優れています。チューブのプロファイルを簡単に曲げたり接合したりできる特殊なレーザーカット機能により、溶接と組み立てが大幅に簡素化され、製品コストの削減に役立ちます。
レーザーを使用すると、オペレーターは 1 つの作業ステップで穴と輪郭を正確に切断できるため、下流プロセスで部品を何度も取り扱う必要がなくなります。特定の例では、鋸引き、フライス加工、穴あけ、バリ取り、および関連するマテリアルハンドリングの代わりにレーザーを使用してチューブ接続を作成することで、製造コストが 30% 削減されました。
コンピュータ支援設計図面からの簡単なプログラミングにより、部品を迅速にプログラムすることができます。レーザー切断たとえ小ロット生産や試作であっても。チューブレーザーは部品を迅速に処理できるだけでなく、セットアップ時間が最小限であるため、部品をジャストインタイムで製造して在庫コストを削減できます。
マシンとアプリケーションのマッチング
切断力。ほとんどチューブレーザー1KW、2KW~4kWの切断力を発揮するレゾネータが装備されています。これは、軟鋼管の一般的な最大厚さ (8mm) とアルミニウムおよびステンレス鋼管の一般的な最大厚さ (6mm) を効率的に切断するには十分です。大量のアルミニウムやステンレス鋼を加工する製造業者は、出力範囲のハイエンドの機械を必要としますが、軽量軟鋼を扱う企業は、ローエンドの機械で十分に対応できる可能性があります。
容量。通常、1 フィートあたりの最大重量で評価される機械の能力も、もう 1 つの重要な考慮事項です。チューブにはさまざまな標準サイズがあり、通常は 6 メートルから 8 メートル、場合によってはそれより長いものもあります。OEM メーカーまたは委託製造業者は、スクラップを最小限に抑えるためにカスタム サイズのチューブを注文するため、一般的な材料サイズに適合する機械を検討する必要があります。ジョブショップの場合、選択はもう少し複雑になります。
材料のロードとアンロード。機械を選択する際のもう 1 つの要素は、原材料を供給できるかどうかです。一般的な部品を切断する一般的なレーザー機械は、手動の装填プロセスが追いつかないほど高速に動作するため、チューブレーザー切断機には通常、最大 8,000 ポンドの束を装填するバンドル ローダーが付属しています。雑誌に資料を掲載します。ローダーはチューブを分離し、1本ずつ機械にロードします。
小規模なジョブのために大規模な実稼働を中断する必要がある場合でも、手動ロード オプションをいくつか用意することが重要です。オペレーターは生産実行を一時停止し、チューブを手動でロードして処理して小さなジョブを完了してから、生産実行を再開します。荷降ろしも関係します。完成したチューブの装置のアンローディング側の長さは通常 10 フィートですが、処理される完成部品の長さに合わせて長くすることもできます。
継ぎ目と形状の検出。溶接チューブはシームレスチューブよりも多くの製品で使用されており、溶接継ぎ目はレーザー切断プロセスや場合によっては最終組み立てを妨げる可能性があります。適切なハードウェアを備えたレーザー機械は通常、溶接の継ぎ目を外側から検出できますが、チューブの仕上げによって継ぎ目が見えにくくなる場合があります。一般的な継ぎ目検知システムは、2 つのカメラと 2 つの光源を使用してチューブの外側と内側を観察し、溶接継ぎ目を検出します。ビジョン システムが溶接シームを検出すると、機械のソフトウェアと制御システムがチューブを回転させ、完成品に対する溶接シームの影響を最小限に抑えます。
ほとんどチューブレーザーシステム円形、正方形、長方形のチューブだけでなく、ティアドロップ形状、山形鋼、C チャネルなどのプロファイルも切断できます。非対称のプロファイルでは、適切にロードしてクランプするのが難しい場合があるため、特別な照明を備えたオプションのカメラがローディングプロセス中にチューブを検査し、検出されたプロファイルに従ってチャックを調整します。これにより、非対称プロファイルの確実な荷重と切断が保証されます。
効率の最大化
値を特定した後、レーザーチューブ切断システム生産プロセスに持ち込むことができる場合は、アプリケーションに合わせてその機器を構成する必要があります。たとえば、ローディング システムが短すぎると、完成部品のネスティング効率に深刻な影響を及ぼし、スクラップが増加する可能性があります。一方、システムが長すぎると、より高い初期投資と必要以上の床面積が必要になります。システム製造元にアドバイスを求めることに加えて、サンプル部品を切断し、利用可能なすべてのオプションを評価して、投資の結果が可能な限り最高の利益を確実にもたらすようにする必要があります。